Construction Equipment License: How to Get Heavy Machinery Operator License in India
April 22, 2025 by admin
Construction Equipment License: How to Get Heavy Machinery Operator License in India
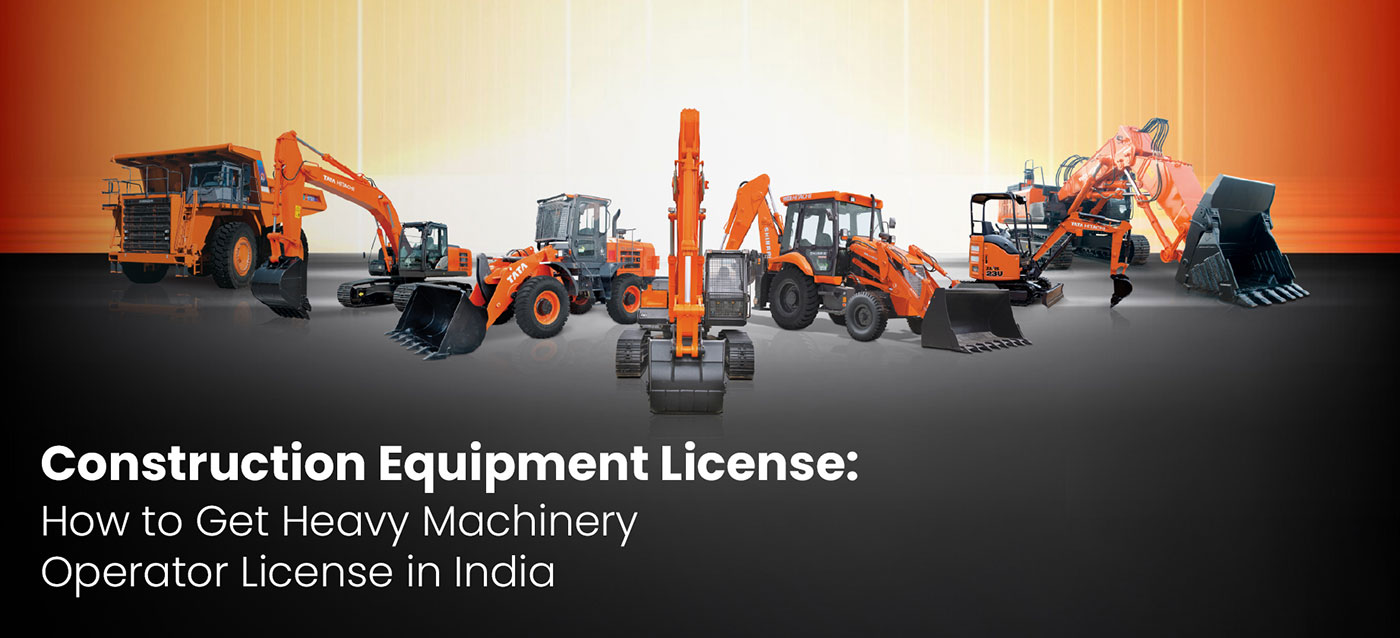
Operating heavy machinery is a crucial role in the construction, mining, and infrastructure industries. In India, becoming a licensed heavy equipment operator requires specific training, certifications, and adherence to legal requirements. If an individual is looking to pursue a career in this field, understanding the process of obtaining a heavy machinery operator license is essential.
Why is a Heavy Machinery Operator License Important?
A heavy machinery operator license ensures that an individual has the necessary skills, knowledge, and safety awareness to operate construction equipment such as excavators,
backhoe loaders,
wheel loaders, bulldozers,
dump trucks and cranes. It minimizes risks of accidents, improves efficiency, and enhances job prospects in industries that require certified operators.
Types of Construction Equipment Requiring a License
In India, operating the following types of heavy machinery typically requires a specialized license:
- Excavators
- Bulldozers
- Cranes (tower cranes / mobile cranes)
- Backhoe Loaders
- Graders
- Road Rollers
- Forklifts
- Pavers
- Dump Trucks
Eligibility Criteria for Obtaining a Heavy Machinery Operator License
Before applying for a construction equipment operator license, one must meet the following eligibility criteria:
- Minimum Age: Typically, applicants must be at least 18 years old.
- Educational Qualification: A basic school education (10th pass) is required in most cases, though higher education may not be mandatory.
- Physical Fitness: Candidates must meet medical fitness requirements, including good eyesight, physical coordination, and reflexes.
- Work Experience (if applicable): Some training institutes and employers require prior work experience or apprenticeship before granting certification.
Committed to skill development and employability,
Tata Hitachi’s skill development program encompasses training for unemployed youth, non-certified operators, dealer staff, and own staff.
Steps to Obtain a Heavy Machinery Operator License in India
Step 1: Enroll in a Recognized Training Institute
To become a licensed heavy equipment operator, individuals must complete formal training from a government-recognized or private training institute. Some prominent institutes include:
- National Academy of Construction (NAC)
- Industrial Training Institutes (ITIs)
- Infrastructure Equipment Skill Council (IESC)
- Central Institute of Road Transport (CIRT)
- Private certified training centers like L&T Construction Skills Training Institute
The training covers both theoretical and practical aspects, including:
- Equipment handling techniques
- Safety protocols
- Maintenance and troubleshooting
- Load calculations
- Operational efficiency
Step 2: Obtain a Learner’s License
Certain categories of construction equipment (like cranes and dump trucks) require a learner’s license before full certification. Applicants must:
- Apply through their respective Regional Transport Office (RTO)
- Pass a written test on traffic rules and basic safety norms
Step 3: Practical Training and Assessment
Hands-on training is a vital part of the certification process. Operators gain real-world experience in handling equipment under supervision. Upon completing training, candidates must undergo an assessment that tests their ability to:
- Operate the equipment safely and efficiently
- Follow industry-standard procedures
- Troubleshoot basic mechanical issues
Successful candidates receive a certificate of competency from the training institute.
Step 4: Apply for a Heavy Machinery Operator License
After completing training and obtaining the necessary certification, the next step is applying for a heavy machinery operator license through the local RTO or relevant industry certification body. The process involves:
- Submitting application forms and documents (ID proof, training certificate, medical certificate, etc.)
- Undergoing a practical driving test (for road-related heavy vehicles)
- Paying the required fees
Once approved, the license is issued, enabling the holder to operate heavy machinery professionally.
Cost of Getting a Heavy Machinery Operator License
The cost of obtaining a license varies based on:
- Training institute fees
- Application and licensing fees
- Medical certification and assessment fees
Validity and Renewal
Heavy machinery operator licenses are usually valid for 3-5 years, after which renewal is required. Operators must:
- Undergo a refresher course (if applicable)
- Submit renewal applications at the RTO
- Pass an updated assessment or medical test
Career Opportunities for Licensed Heavy Equipment Operators
A certified heavy equipment operator can find employment in various industries, such as:
- Construction: Infrastructure projects, road construction, and real estate development
- Mining: Coal, iron ore, and mineral excavation sites
- Logistics and Warehousing: Forklift operation in industrial storage facilities
- Government Projects: Railways, metro projects, and public sector construction
Conclusion
Getting a heavy machinery operator license in India is a structured process involving training, assessment, and certification. With the increasing demand for skilled equipment operators in infrastructure and construction, obtaining a license enhances employability and ensures safe operations.
Fuel Efficiency Tips for Excavators: How to Lower Your Heavy Equipment Operating Costs
April 21, 2025 by admin
Fuel Efficiency Tips for Excavators: How to Lower Your Heavy Equipment Operating Costs
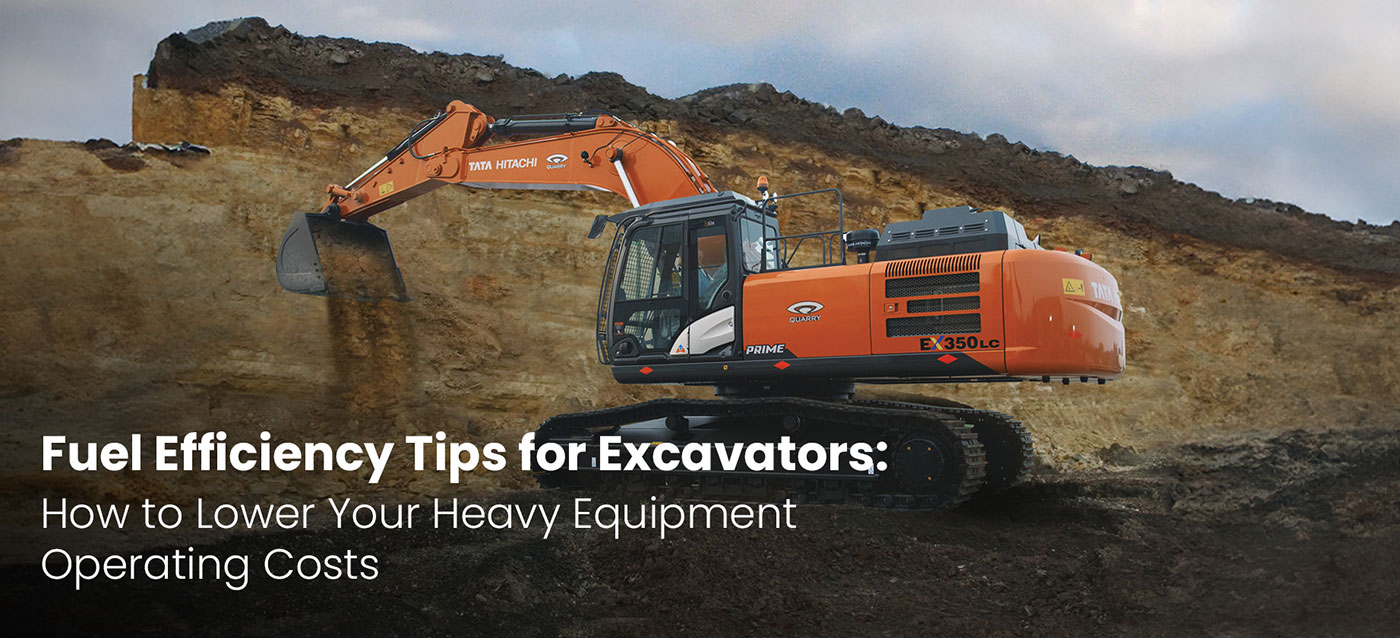
Fuel efficiency is a top priority for construction businesses, as fuel expenses often account for a significant portion of operating costs. Below are practical strategies to enhance the fuel efficiency of your excavators and reduce overall operating costs.
Maintain Your Excavator for Optimal Performance
A well-maintained machine consumes less fuel and operates more efficiently. Key maintenance tips include:
- Regularly servicing the engine and hydraulic systems.
- Keeping air filters clean to prevent fuel wastage.
- Ensuring proper track tension to reduce drag and wear.
Utilize Modern Technology
Advancements in technology provide tools to monitor and optimize fuel usage. Consider:
- Telematics systems: These provide real-time data on fuel consumption and machine performance.
- Automatic idle shut-off: Reduces unnecessary fuel consumption during inactivity.
- Eco-modes: Adjust machine settings to balance power and efficiency.
Adopt Smart Operational Practices
How an excavator is operated can significantly impact its fuel consumption. Best practices include:
- Reducing idle time: Turn off the engine during prolonged inactivity.
- Optimizing machine settings: Use appropriate power modes based on the task.
- Planning operations efficiently: Minimize unnecessary movement and prioritize tasks.
Use High-Quality Fuel and Lubricants
Investing in premium fuel and lubricants can improve combustion efficiency and reduce wear. Ensure:
- Fuel is free from contaminants.
- Lubricants meet the manufacturer’s recommendations.
Train Operators
Well-trained operators can significantly reduce fuel consumption. Training programs should cover:
- Proper use of controls to avoid overworking the engine.
- Techniques to minimize repetitive movements.
- Awareness of fuel-saving practices.
Monitor Fuel Consumption
Keeping track of fuel usage helps identify inefficiencies. Use:
- Fuel logs to record consumption over time.
- Alerts to signal abnormal usage patterns.
- Reports generated by telematics systems for actionable insights.
Schedule Regular Inspections
Frequent inspections ensure all components function efficiently, reducing unnecessary fuel use. Focus on:
- Identifying leaks in fuel lines or hydraulic systems.
- Monitoring tire or track conditions for optimal traction.
By following these tips, you can significantly lower the operating costs of your excavators while contributing to a more sustainable construction environment. Small changes in operational and maintenance habits can lead to substantial savings in the long run.
Unearthing the Power of Excavators: A Comprehensive Guide to Types and Applications
March 28, 2024 by admin
Excavator: Types, Specifications, Uses in Construction Site
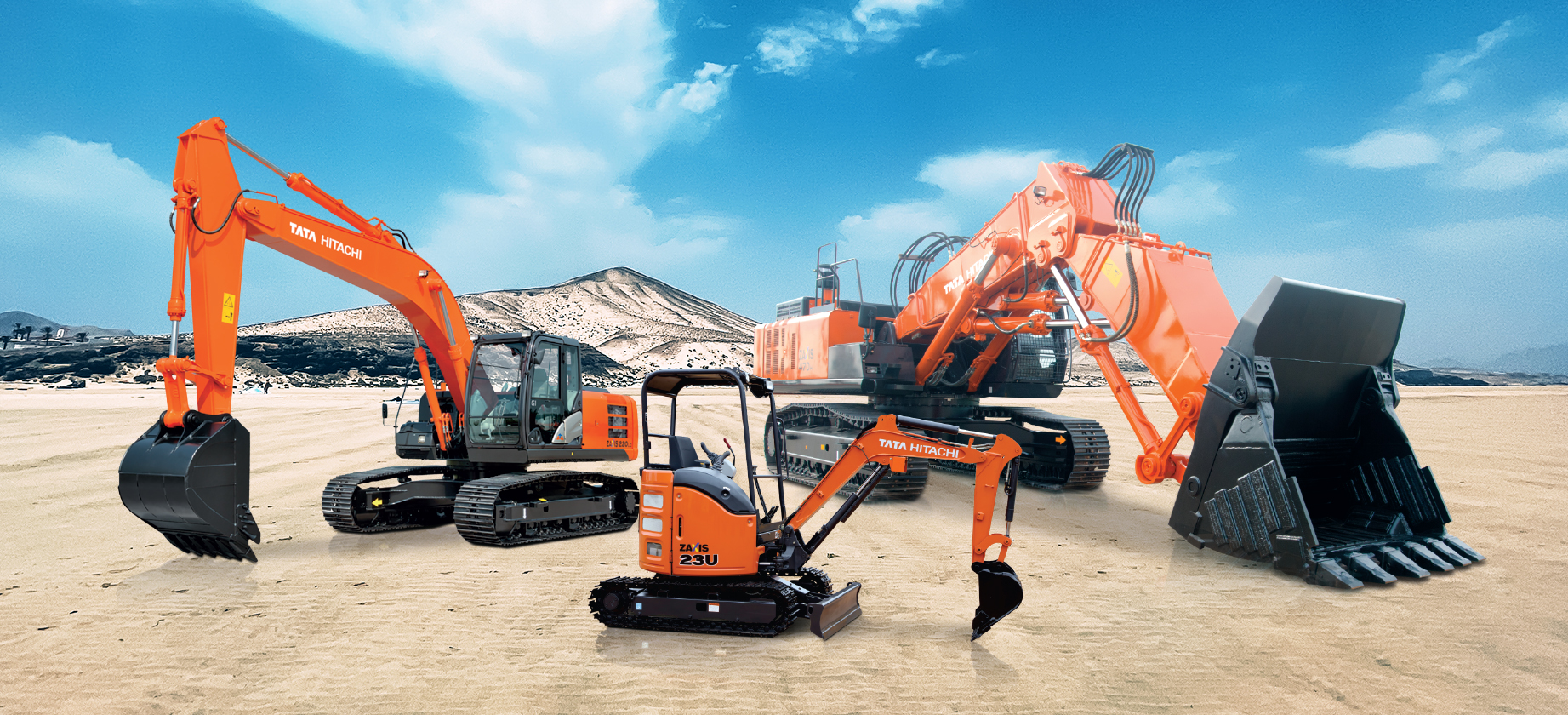
Excavators have revolutionized the construction and mining industries, providing unparalleled efficiency in earthmoving, digging and excavating. These heavy-duty machines have powerful arms and buckets that can move substantial amounts of soil, rocks, and debris.
The essence of an excavator lies in its ability to transform the physical environment. With their robust structures and hydraulic systems, these machines possess unmatched strength and agility to tackle various excavation tasks. They are the workhorses of the construction site, tirelessly moving earth and materials to create the foundations, trenches, and structures that form the basis of our built world.
Equipped with attachments, such as buckets, breakers, and grapples, excavators adapt to various needs and applications. They can effortlessly demolish structures and clear land with precision and control. From small-scale projects in urban areas to colossal mining operations, excavators have become indispensable in meeting the challenges of diverse industries. In this blog, we will explore the meaning of excavators and delve into various types, their unique features, and their detailed applications. Understanding the capabilities and uses of different excavator types will shed light on their significance and versatility in modern-day projects.
Different Types of Excavators Offered by Tata Hitachi
-
Mini Excavators: Compact Warriors
Excavators that are smaller in size than their bigger equivalents are referred to as mini excavators or compact excavators. Typically weighing approximately less than 4000 kg, mini excavators offer exceptional maneuverability. Their compact size allows access to areas inaccessible to larger machines. Mini excavators find extensive applications in landscaping, urban construction, utility work, and small-scale projects. They are commonly employed in projects for digging trenches, installing irrigation systems, and shaping the terrain. In urban construction, mini excavators excel at tasks such as demolishing small structures, digging foundations for small buildings, and handling materials on cramped job sites. Additionally, they are valuable in utility work, including installing and repairing sewer lines, electrical cables, and plumbing systems. With their versatility and maneuverability, mini excavators offer tremendous value in various applications that require precision and efficiency in confined areas.
-
Construction Excavators: The Backbone of Building
Construction excavators are the most commonly used excavators in the construction industry. They come in various sizes, from compact models to large machines weighing approximately 38,000 kg. These versatile machines are employed for digging trenches, excavating foundations, and moving large volumes of earth. With their powerful arms and buckets, construction excavators efficiently handle materials, including soil, rocks, and debris. They are also utilized for demolishing structures and clearing land. The ability to adapt to different attachments, such as breakers, grapples, and augers, further enhances their capabilities, allowing them to perform specialized tasks. Construction excavators are crucial instruments that aid in effectively completing projects in the construction sector, whether erecting structures, preparing construction sites, or enabling infrastructure development.
-
Mining Excavators: Unearthing Earth’s Riches
Mining excavators are heavyweight machines specifically designed for excavation and earthmoving in mining operations. These robust machines are engineered to withstand demanding mining conditions and efficiently handle colossal amounts of material. Mining excavators range from medium-sized machines to colossal units weighing over 800 metric tons. They feature reinforced structures, sturdy buckets, and advanced technologies for increased productivity and reliability. Mining excavators play a pivotal role in open-pit mining, where they remove overburden (soil and rock covering valuable minerals), extract minerals, and load them onto trucks for transportation. With their massive capacity and power, mining excavators significantly contribute to extracting and processing various minerals, including coal, iron ore, gold, and copper.
Other Specialized Excavators: Meeting Unique Challenges
Apart from mini, construction, and mining excavators offered by Tata Hitachi, several specialized excavator types are designed for specific tasks. These include:
-
Dragline Excavators
Dragline excavators are heavy machinery used in large-scale mining and civil engineering projects. They employ a dragging mechanism to excavate material, such as soil, rocks, and minerals. The main distinguishing feature of dragline excavators is their long boom and wire ropes, which enable them to reach great distances. These massive machines are typically used in open-pit mining operations, where they remove overburden (soil and rock covering valuable minerals), extract minerals, and load them onto trucks for transportation. Dragline excavators offer high productivity and efficiency, making them essential for extracting resources on a large scale.
-
Wheel Excavators:
Wheel excavators are a type of excavator that features wheels instead of tracks for mobility. These machines offer greater speed and maneuverability, making them well-suited for road construction, urban development, and other applications requiring quick mobility. The wheel excavators are equipped with a rotating platform, an arm, and a bucket, allowing them to efficiently dig, lift, and move materials. Their wheel configuration enables them to easily navigate paved surfaces and uneven terrain, making them versatile for various construction projects.
-
Long-Reach Excavators:
Long-reach excavators, also known as long-reach booms or high-reach excavators, are specialized machines designed with extended arms and booms to reach farther distances than conventional excavators. These excavators are particularly useful in applications that require deep digging, dredging, or demolition work. With their extended reach capabilities, they can efficiently access difficult areas, such as deep trenches, high embankments, or tall structures. Long-reach excavators enable operators to perform tasks precisely, maintaining stability and control while operating at extended distances. Their versatility makes them valuable assets in projects involving waterway maintenance, bridge construction, deep excavation, and selective demolition, where traditional excavators may not have the necessary reach to complete the job effectively.
-
Suction Excavators:
Suction excavators are specialized excavator types that employ powerful suction mechanisms to delicately remove material from the ground. These machines utilize a combination of high-pressure water jets and vacuum systems to dislodge and extract soil, rocks, and debris without causing damage to underground utilities or fragile structures. Suction excavators are particularly valuable in tasks that require precision excavation, such as uncovering buried utilities, working in congested urban areas, and conducting archaeological digs. Their ability to excavate with minimal disruption and a reduced risk of damage makes them an essential tool in projects where safety, accuracy, and preservation are paramount.
Excavators: Powerful Machine for Efficient Earthmoving and Safety Tips
by admin
Excavator Safety Tips, Operations in Construction Site
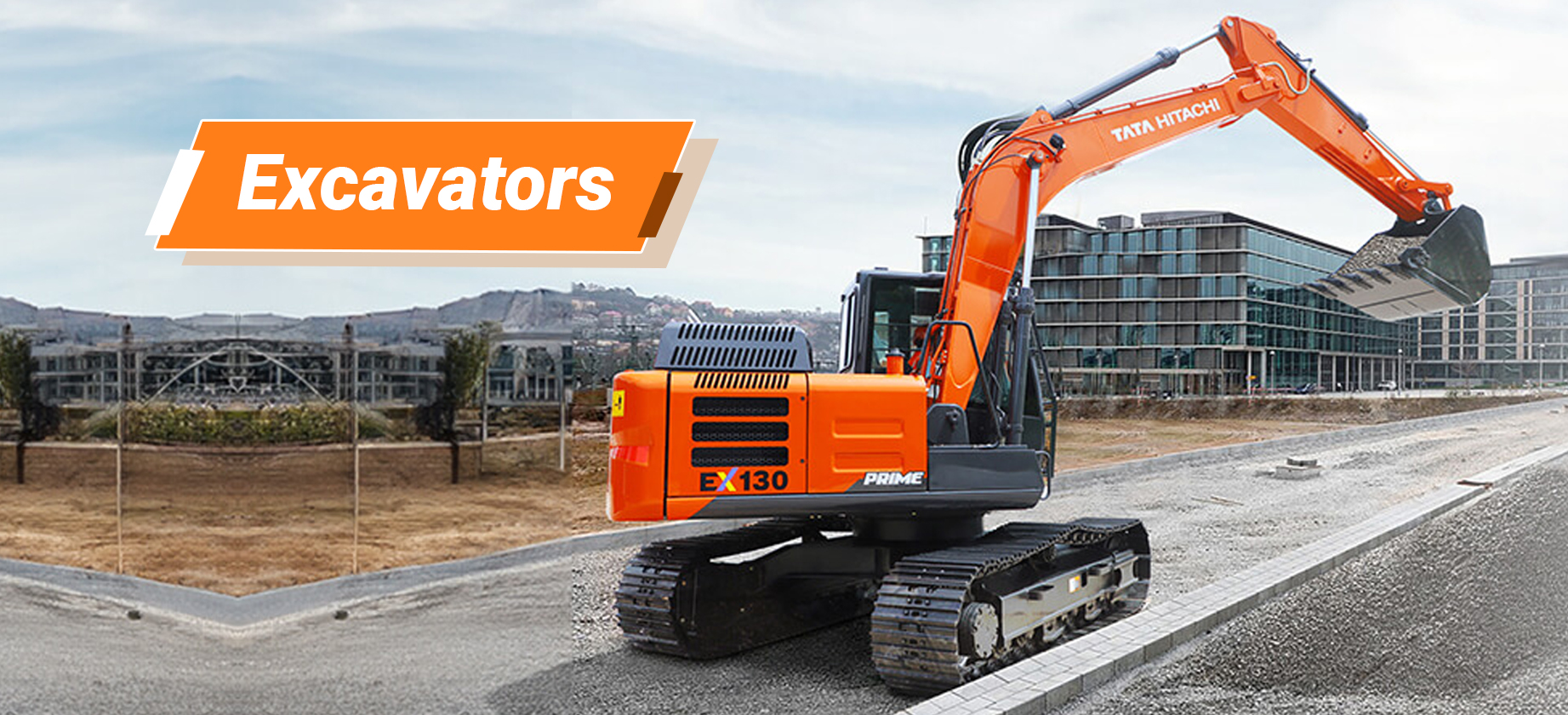
Excavators are robust and versatile machines that play a vital role in construction, mining, and excavation projects. With their hydraulic power and specialized attachments, excavators can perform various tasks, from digging trenches to demolishing structures. This article will discuss excavator operating and key safety tips to create a secure working environment.
HOW TO OPERATE AN EXCAVATOR
Operating an excavator requires skill, knowledge, and adherence to safety protocols. Here is a detailed explanation for an excavator operator on how to operate an excavator effectively:
- Familiarization of Controls: Before operating the excavator, take the time to become familiar with the machine’s controls. These typically include control levers to move the hydraulic arm and bucket, foot pedals for the tracks (crawlers) and various switches for auxiliary functions. Refer to the operator’s manual for the specific layout and functions of the controls on your excavator model.
- Perform Pre-Operational Checks: Before starting the excavator, conduct thorough pre-operational checks. Inspect the machine for any visible damage, leaks, or loose components. Please report any problems or malfunctions immediately and wait to use the machine until it has been given the all-clear validation.
- Cabin Layout and Visibility: To operate the excavator, familiarize yourself with the cabin’s layout and the location of essential controls and instruments. Ensure that all windows are clean and provide clear visibility of the surroundings.
- Starting the Excavator: The excavator’s engine follows the manufacturer’s instructions. Before beginning operations, give the machine some time to warm up. Monitor the engine’s temperature and pressure gauges to ensure they are within the recommended range.
- Controlling the Excavator’s Movements: Use the control levers to manipulate the hydraulic arm and bucket. Familiarize yourself with the controls’ sensitivity and range of motion to achieve precise movements.
- Digging and Excavation: Position the excavator close to the digging area, ensuring stability on level ground. Use the controls to lower the bucket into the ground, applying gradual pressure to break the soil or rocks. Control the arm’s movements to excavate the desired depth and shape the trench or hole as required. Remember to maintain stability by keeping the machine balanced and avoiding excessive movements that could lead to tipping off.
- Lifting and Moving: Position the bucket or the appropriate attachment over the load to lift materials, ensuring proper balance and weight distribution. Use the controls to lift the load slowly, keeping it close to the ground to maintain stability. Move the excavator smoothly and steadily while carrying the load, ensuring clear visibility of the surroundings. Avoid swinging the load excessively, as it can compromise stability and safety.
- Dumping and Loading: When dumping the load, position the bucket or attachment over the desired location and carefully release the material. When loading materials onto trucks or stockpiles, ensure the excavator’s stability and the receiving area. Avoid overloading the bucket or attachment beyond its specified capacity.
SAFETY TIPS FOR EXCAVATOR OPERATION:
Operating an excavator requires strict adherence to safety guidelines. By implementing essential excavator safety tips, excavator operators can maximize productivity while ensuring a secure working environment for themselves and others on the job site. Here are some crucial safety tips to consider:
- Operator Training: Ensure that operators receive proper training on excavator operation, including safety procedures, controls, and maintenance. Ongoing training and certification programs can enhance skills and knowledge, ensuring safe and efficient operation.
- Personal Protective Equipment (PPE): Always wear the proper personal protection gear, such as a hard helmet, reflective clothes, etc. PPE helps protect against potential hazards and minimizes the risk of injuries.
- Safe Access: Use the provided steps, handrails, and handholds when entering or exiting the excavator’s cabin. Avoid jumping or climbing on or off the machine, as it can lead to slips, trips, and falls.
- Secure Work Area: Before operating the excavator, ensure the work area is clear of personnel, obstacles, and underground utilities. Mark and identify buried pipes, cables, or infrastructure to prevent accidents and damage.
- Stability and Slopes: Assess the ground conditions before operating the excavator, especially in soft or unstable soil areas. Avoid operating on slopes that exceed the machine’s recommended limits to prevent tipping accidents.
- Bucket and Attachment Safety: Use the excavator’s bucket and attachments within their specified capacity limits. Overloading can compromise stability and lead to accidents. Ensure proper attachment installation and secure all pins and fasteners before operation.
- Safe Distance: Keep bystanders and other workers safe during excavator operations. Use caution when swinging the boom or moving the machine, as the swinging radius can pose a hazard to those nearby.
- Refueling, Maintenance and Inspection: Follow proper procedures for refueling the excavator, including turning off the engine and avoiding smoking or open flames in the vicinity. Adhere to maintenance schedules and perform routine inspections to ensure smooth excavator operations.
- Insurance for Excavator: It is strongly recommended to have insurance coverage for an excavator. This coverage will help mitigate financial losses in accidents, damages to the excavator, third-party injuries or property damage, theft, vandalism, and other unforeseen circumstances. Insurance ensures the equipment is financially protected against potential liabilities and costs arising during its use.
Wheel Loader Vs Excavator: Unveiling the Differences and Choosing the Right Equipment
March 4, 2024 by admin
Wheel Loader Vs Excavator: Unveiling the Differences and Choosing the Right Equipment
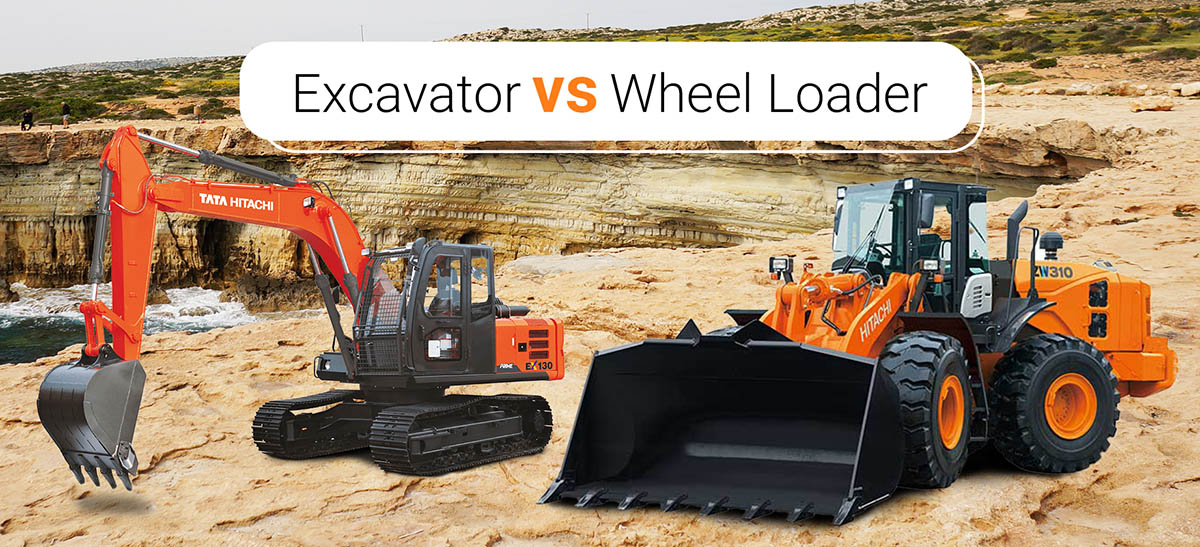
In the world of construction and earthmoving equipment, two indispensable machines are the wheel loader and the excavator. Each of these machines has its unique characteristics and excels in specific tasks. This blog will briefly overview each piece of equipment individually, detail their differences, and suggest which equipment suits different situations. By the end, you will have a clear understanding of these machines and be able to make an informed decision when selecting the right equipment.
WHEEL LOADER
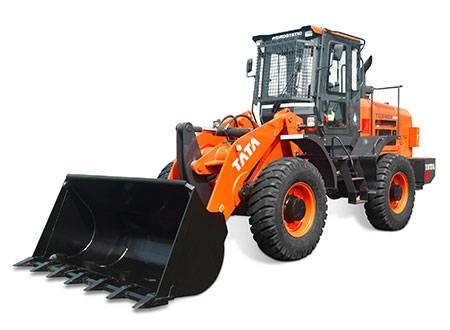
The
wheel loader is a versatile machine designed primarily for material handling tasks. It features a large front-mounted bucket attached to hydraulicly operated arms that can be raised and lowered. The key
features of a Wheel Loader are that they excel in loading, carrying, and dumping various materials such as soil, gravel, sand, or debris. They are commonly used in construction sites, material handling yards, and recycling centers. Wheel loaders have powerful lifting powers that enable them to move huge loads easily. The front-mounted bucket can be replaced with attachments, such as forks, grapples, or snow ploughs, making the wheel loader adaptable to different tasks.
EXCAVATOR
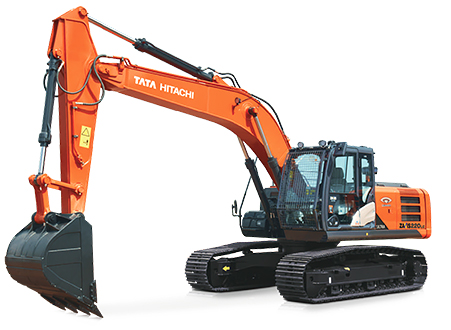
An excavator is a heavyweight machine designed for digging, excavation, and demolition. It features a long boom arm with a bucket attached at the end, capable of extensive movement and precise operations. Excavators have tracks or wheels, providing stability and mobility on various terrains. An excavator’s key features are that they are specifically designed for digging, trenching, and excavation tasks. They can reach deep into the ground and perform precise operations, making them invaluable in construction projects, utility work, and landscaping. It comes with various attachments, including specialized buckets,
rock breakers, grapples, and
augers, expanding their functionality and making them adaptable to different tasks. An excavator’s wide tracks stabilize uneven terrains, ensuring efficient operation.
DIFFERENCES BETWEEN WHEEL LOADERS AND EXCAVATORS:
Wheel Loaders:
Wheel loaders are typically utilized as material handling equipment. They are skilled in scooping, lifting, and moving large items like gravel, sand, and building materials. Materials may be stockpiled, moved about the construction site, or loaded into trucks using the machine’s front-mounted bucket. Wheel loaders can readily maneuver on various terrains, including uneven ground, because of their huge wheels or tyres. Wheel loaders are appropriate for activities requiring regular relocation since they can move around the work sites. Their primary priority is effective material management, not deep excavation. Due to their adaptability, wheel loaders are excellent for various jobs, such as mining, construction, forestry work, recycling operations and waste management.
Excavators:
Excavators are generally made for excavation, demolition, and digging jobs. They are excellent for removing tonnes of dirt, pebbles, and other ground detritus. Their hydraulic arms and bucket allow
excavators to dig deep holes, lay foundations, and complete delicate digging tasks. They are frequently employed for heavy lifting, grading, and site preparation. On the other hand, an excavator’s design is longer, crawler-based, and features a rotating cabin and a hydraulic arm. Instead of wheels, they use tracks, which offer stability and better maneuverability on soft or uneven terrain. Deep digging, precision trenching, and operating in limited places are jobs that excavators excel at. Excavators are made especially for deep digging tasks. They can reach far into the earth because of the hydraulic arm’s ability to extend to enormous depths. Excavators are versatile tools that may be fitted with a variety of attachments. Different-sized buckets,
hydraulic rock breakers for demolition operations, and specialized equipment like shears or
augers are common attachments. Thanks to their adaptability, Excavators can adapt to various jobs, including excavation and demolition, as well as forestry, mining, and road building.
SUITABILITY IN DIFFERENT SITUATIONS:
Wheel Loaders:
- Material handling: Regarding material handling, wheel loaders are the best choice for jobs that need scooping, lifting, and moving items like gravel, sand, and waste.
- Quick transfer: Wheel loaders are appropriate for activities requiring frequent transfer within the job site due to their mobility and maneuverability.
- Versatility: Wheel loaders have a number of attachments that can be added to increase their functionality for jobs and operations.
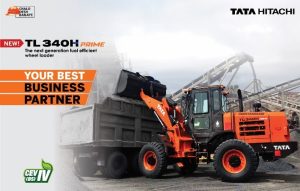
Excavators:
- Deep Digging: Excavators are excellent in deep-digging jobs like building foundations, trenching, or removing tonnes of dirt, rocks, and even waste.
- Precision and Reach: Excavators can dig precisely and intricately because of their rotating cabin, hydraulic arm, and ability to reach enormous depths.
- Limited Space: Their crawler-based construction allows excavators to operate in small and remote locations, making them ideal for tasks requiring precision maneuvering.
- Flexibility: Excavators are versatile and may be fitted with various attachments, enabling them to carry out jobs other than excavation, such as earthwork, solid waste management, canal cutting, forestry work, and road building.
The decision between a wheel loader and an excavator ultimately comes down to the project’s unique requirements, the duties involved, the nature of the terrain, and accessibility issues. The best machine for the task will be determined by weighing these considerations.
EX 130 Prime
January 20, 2024 by admin
ZAXIS 140H Ultra
by admin
EX 200 Infra
January 18, 2024 by admin
EX 200LC Prime
January 17, 2024 by admin
EX 210 Infra
January 16, 2024 by admin